Robot Ballet | Kyle Huber
- E3 Bloggers
- Jun 19, 2018
- 2 min read
Updated: Jun 23, 2018

Today was a special adventure for the E3 students. We were going to Disneyland! Specifically, we were going to Disneyland for Engineers. We left Berlin early in the morning and took a long, comfortable train ride through the lush, German countryside. We arrived in Wolfsburg right around 10 a.m. and immediately beheld the monolithic, domineering red-brick building right by the train stop. Wolfsburg is a city built by Volkswagen, for Volkswagen. It is a testament to the history-rich and innovative company. We were all excited to tour this impressively large factory, but we had yet to learn the true magnificence of the cutting-edge facility at the forefront of automotive manufacturing technology.
Hassan, our Kenyan tour guide, began by giving us a short lesson on the substantial history of Volkswagen Wolfsburg – a factory that focused on efficiency and productivity above all else while building “the people’s car”. The automotive powerhouse had some perplexing numbers to boast: the Wolfsburg Factory opened on May 26, 1936 and is the largest automotive factory in all of Europe with 62,000 permanent staff members. Under current operating specifications, 3,500 cars are produced at the factory each day with a full capacity of 3,800 cars/day possible. This corresponds to a new car being produced every 18 seconds.
After the brief introduction, Hassan rallied our pack onto the touring caravan – a bundle of carts, with plush seats I might add, all toted by a custom Volkswagen car. With plenty of light humor adorning the way, Hassan zoomed through the factory while doing his best to explain the mesmerizing sites and scenes all around us. Imagine giant, arm-like robots zipping back and forth in their designated zones preparing and zapping car parts and panels at an impressive, fluid pace, and one might get a glimpse of what touring Volkswagen Wolfsburg was like. Each robot was a ballet dancer on an industrial stage. Each movement was an elegant display of graceful choreography and incredible precision – 1/10 of a millimeter to be exact.
Humans worked alongside and moved with similar tactful and precise gestures as their robot colleagues. In this cyber-physical environment, beautiful and striking cars of all shapes and colors were birthed on production lines in just 22 hours. In a myriad of production areas but following a single line, the body panels were assembled together into the whole car body frame and inspected for utmost quality. Following this, each body took a plethora of baths before being painted in one of Volkswagen’s 22 colors. In a graceful marriage, the car body and drive train were then unified, while doors, interior features, and logos came later. Finally, after the entire fascinating process, a strikingly elegant Volkswagen car was finally ready for extensive quality inspections and testing before hitting the market.
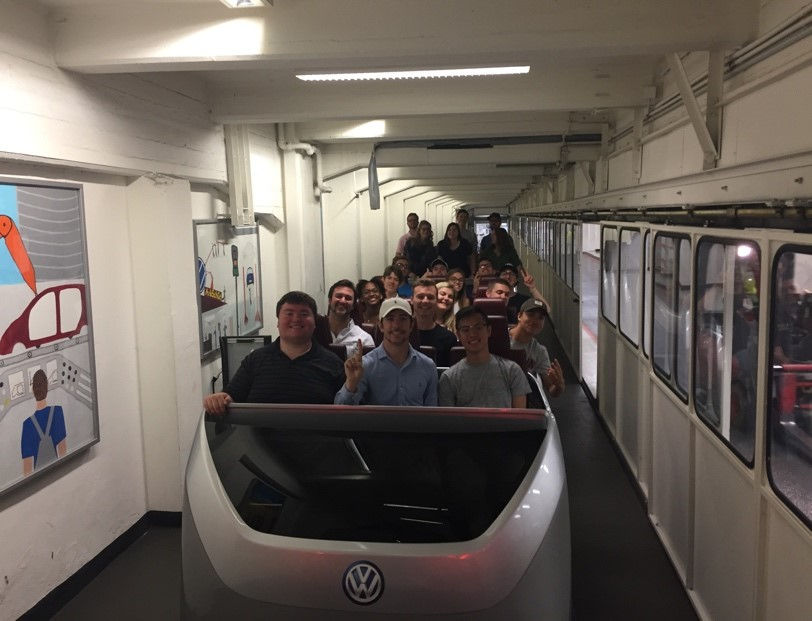
This entire process, and the facility that incubated it, was nothing shy of a marvelous example of humanity’s technological potential. As an engineer, I found excitement with each striking spectacle that adorned the tour while having a deep appreciation for the dedication of the developers that designed the factory and its intricacies as well as the craftsmen that made the automotive production lines successful.
Comentarios